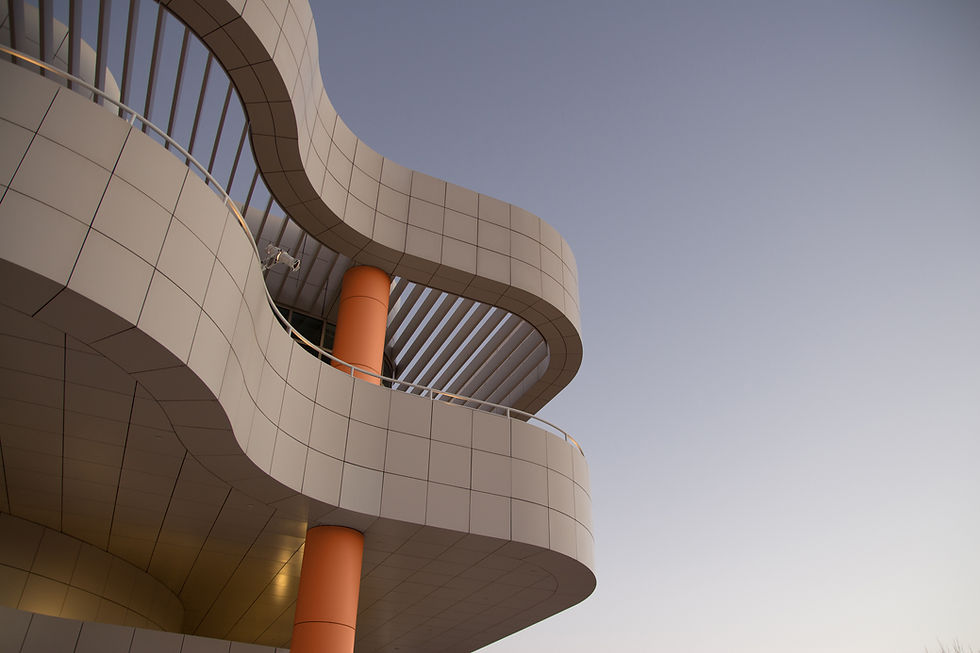

Arc Flash Label Requirements: A Comprehensive Guide
Arc flash incidents are one of the most dangerous electrical hazards in industrial and commercial settings, and they can result in severe injuries or fatalities. To mitigate these risks, it's essential to comply with the latest regulations and standards, particularly the NFPA 70E, which outlines the requirements for arc flash labeling. This paper provides a comprehensive overview of arc flash label requirements, the equipment that must be labeled, and other pertinent details to ensure compliance and safety in your facility.
1. Understanding Arc Flash Labels
Arc flash labels are crucial safety tools that provide essential information about the arc flash hazards present in electrical equipment. These labels serve to inform and protect workers by detailing the specific risks and precautions needed when interacting with electrical equipment.
Key Elements of an Arc Flash Label
According to NFPA 70E 2024 (the most current edition as of the date of this writing), an arc flash label must include the following elements:
Arc Flash Warning Header: A clear and visible "WARNING" or "DANGER" header to indicate the presence of an arc flash hazard. The choice between "WARNING" and "DANGER" depends on the severity of the hazard, with "DANGER" being used for more severe hazards.
Nominal System Voltage: The label must indicate the nominal voltage of the electrical system. This is critical for understanding the potential severity of an arc flash event.
Arc Flash Boundary: The distance from the source of the arc flash within which a person could receive a second-degree burn. This boundary must be clearly stated in feet and inches (or metric units).
Incident Energy at the Working Distance: The incident energy level, typically measured in calories per square centimeter (cal/cm²), at the specified working distance. This value helps determine the required Personal Protective Equipment (PPE).
PPE Category: The label should include the PPE category (from 1 to 4) or the specific PPE required to protect against the calculated incident energy. If the PPE category method is used, refer to the appropriate tables in NFPA 70E.
Working Distance: The distance between the worker and the point of the arc flash. This is typically provided in inches or millimeters and is critical in calculating the incident energy.
Date of Analysis: The date on which the arc flash risk assessment was conducted. This is important for ensuring that the data is current and that the label reflects the latest conditions and equipment configurations.
Equipment Identification: A unique identifier for the piece of equipment, such as a panel number or machine name. This aids in ensuring that the label is correctly applied to the right piece of equipment.
Optional but Recommended Elements
Shock Hazard Information: Including information about shock hazards, such as voltage levels and approach boundaries, is recommended but not strictly required by NFPA 70E. This information can further enhance worker safety by informing them of all potential electrical hazards.
Arc Flash Risk Assessment Notes: Any additional notes or details from the arc flash risk assessment that could provide context or further guidance to workers.
2. Equipment Requiring Arc Flash Labels
NFPA 70E mandates that all equipment likely to require maintenance or examination while energized must be labeled with an arc flash warning. The following types of equipment typically require arc flash labels:
Electrical Panels and Switchboards: All types of electrical panels and switchboards that are likely to be serviced or examined while energized must be labeled. This includes main distribution panels, subpanels, and any other panels that control significant electrical loads.
Motor Control Centers (MCCs): MCCs, which house motor starters, circuit breakers, and other control equipment, must have arc flash labels. These are often high-risk areas due to the concentration of electrical circuits.
Transformers: Pad-mounted, dry-type, and liquid-filled transformers, especially those located within accessible areas, should be labeled. Transformers can present significant arc flash hazards during maintenance or troubleshooting.
Disconnects and Circuit Breakers: Disconnect switches, fused disconnects, and circuit breakers, including those integrated into panels or standalone, must be labeled. These devices often require operation while energized, making labeling crucial.
Bus Ducts and Busways: Bus ducts and busways that distribute power across a facility need arc flash labels, especially at points where sections are connected or tapped.
Automatic Transfer Switches (ATS): Given that they are involved in switching between power sources, often under load, ATS units must be labeled to indicate the arc flash hazards present.
Generators: Standby and emergency generators, particularly those with integrated circuit breakers or disconnects, should be labeled. Maintenance and testing of these units can expose workers to arc flash hazards.
Control Panels and Enclosures: Any control panel or enclosure that might require opening for maintenance, troubleshooting, or programming should have an arc flash label, especially if it houses exposed live parts.
Variable Frequency Drives (VFDs): VFDs, due to their complex electronics and high current handling, should be labeled to indicate the arc flash risk during maintenance or inspection.
Power Distribution Units (PDUs): Common in data centers and other critical environments, PDUs must be labeled as they are central to power distribution and often require live work.
Industrial Machinery: Any industrial machinery that operates with significant electrical power and could require live maintenance should have arc flash labels. This includes machinery with integrated control panels, motors, and other electrical components.
3. Labeling Best Practices
To ensure that arc flash labels are effective and compliant with NFPA 70E, consider the following best practices:
Durability and Visibility: Labels must be durable enough to withstand the environmental conditions of the facility (e.g., moisture, dust, UV exposure). They should be made from materials resistant to wear and tear and should remain legible for the lifespan of the equipment.
Consistent Placement: Place labels at eye level on the equipment’s access point or enclosure door. If the equipment has multiple access points, ensure each one is labeled.
Review and Update Labels Regularly: Arc flash risk assessments should be reviewed every five years or whenever significant changes are made to the electrical system. Labels must be updated to reflect any changes in equipment configuration, fault current levels, or protective device settings.
Employee Training: Workers should be trained to understand and comply with the information on arc flash labels. This training should be part of the facility's overall electrical safety program.
Coordination with Facility Maintenance: Coordinate with facility maintenance teams to ensure that labels are not removed or obscured during routine maintenance. Labels should also be checked for legibility and replaced if they become damaged or faded.
4. Compliance with Other Standards and Regulations
While NFPA 70E is the primary standard governing arc flash labeling, compliance with other standards is also essential:
OSHA Regulations: OSHA enforces electrical safety in the workplace, and compliance with NFPA 70E helps ensure adherence to OSHA’s broader safety regulations. OSHA requires employers to provide a workplace free from recognized hazards, including electrical hazards.
IEEE Standards: IEEE 1584 provides the methodology for calculating arc flash incident energy and defining the arc flash boundary. Labels should reflect calculations based on the latest IEEE 1584 standards to ensure accuracy.
NEC (National Electrical Code): The NEC requires proper labeling of electrical equipment, including marking requirements for arc flash hazards. Ensuring compliance with the NEC is essential for both safety and code compliance.
5. Conclusion
Arc flash labeling is a critical component of an effective electrical safety program. By adhering to the latest NFPA 70E requirements, facilities can significantly reduce the risk of arc flash incidents and protect workers from potentially life-threatening hazards. Proper labeling, combined with regular risk assessments, employee training, and adherence to other relevant standards, forms the foundation of a robust safety strategy in any facility handling electrical equipment.
For more detailed guidance or assistance with arc flash analysis and labeling, Powersafe Engineering is here to help. We offer expert services to ensure your facility is fully compliant and your workers are safe from electrical hazards.
Contact us today at PowerSafe Engineering!
#ArcFlashSafety #ElectricalSafety #NFPA70E #ArcFlashLabels #ElectricalEngineering #WorkplaceSafety #SafetyCompliance #OSHA #IEEE1584 #IndustrialSafety #PPE #ElectricalHazards #SafetyFirst #PowerSystems #PowersafeEngineering #SafetyStandards #FacilitySafety